You have to keep in mind that there is no such glove that protects against all risks. It is therefore necessary to specify the need“. Choosing the right cut-resistant gloves is essential for ensuring safety and efficiency in various industries, from construction to food processing. With many options available, it’s important to consider several factors to select the gloves that best meet your needs. Here’s a guide to help you make the right choice.
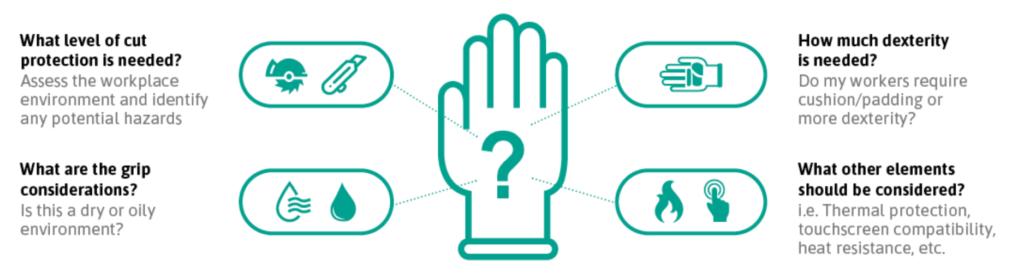
1. Understand the Cut Resistance Level
Cut-resistant gloves are rated based on their ability to withstand cuts. The most common rating system is the CEEN388:2016 standard. The first test, known as the “Couptest“, is used to assess the resistance to a repetitive and prolonged but low-intensity cut. This test is particularly useful for people who constantly handle small metal or glass parts, the automotive industry, mechanics, etc.
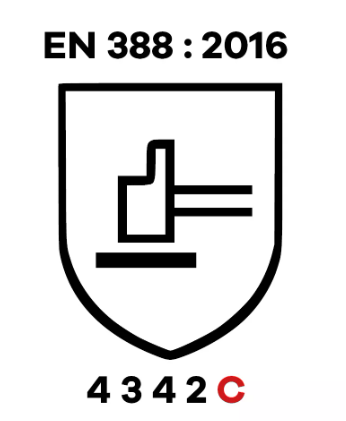
The 2nd test is called the “TDM test” related to ISO 13997. This test methods is very similar to the ANSI/ISEA 105 cut test, which rating from A1 to A9.
This test performed with a straight blade evaluates the resistance of a material to a short, dry cut with an applied force of varying intensity ranging from 2 to 30N. The “TDM test” is a good performance indicator for accidental risks such as blows from a cutter or accidents related to carrying sharp, heavy and slippery objects: glass or steel plates. At the end of the “TDM test”, a performance level from A to F is then assigned to the glove.
Assess the level of risk in your work environment to determine the appropriate rating. For example, B-C CUT LEVEL gloves are suitable for light-duty tasks, while D-F gloves are ideal for handling sharp materials like glass or metal.
Generally EN ISO 13977 A EQUALS ANSI A1, B TO A2, C EQUALS A3, D EQUALS A4, E QUALS A5, AND F EQUALS A6 ABOVE.

2. CHOOSING GLOVES MATERIALS
You should also assess the material used to line the gloves.
Each type of fiber has properties that determine which glove is the best choice for your staff. Often the lining is a combination of the fibres listed below.
Aramid
Looking for a glove with medium-cut resistance? Then a specimen lined with the material aramid is a very suitable choice. Well-known brand names are Kevlar and Twaron.
A lining made of this material is resistant to heat, but less resistant to abrasion and UV radiation.
HPPE
When the gloves do not need to be heat-resistant, a liner made of HPPE is a very suitable choice. HPPE is a material based on polyethylene.
Like aramid, HPPE has medium cut resistance. The wearing comfort is also good. Furthermore, HPPE offers sufficient abrasion resistance.
Fiberglass
Fibreglass makes other liner fibers more resistant to cuts. A liner is usually not made of just fiberglass.
The disadvantage of fiberglass is that it can break when the glove is used for a long time. If that happens, the cut resistance of the glove may be lowered.
Stainless steel
The material stainless steel is suitable for the lining, especially if it is mixed with HPPE.
However, like fibreglass, stainless steel can break and become less resistant to cuts.
The wearing comfort of a glove lined with stainless steel is average. So, it is less suitable for wearing the entire workday.
Coatings of cut resistant gloves
When buying gloves, also pay attention to the coating.
The raw material of the coating determines the glove’s grip, among other things. Do you work with a slippery liquid, such as oil? Then you need gloves with an exceedingly good grip to prevent sharp objects from slipping out of your hands.
In other working conditions, a supple coating is particularly important.
The most common coatings used on cut-resistant gloves and the properties of each material are listed below.
Polyurethane (PU)
Gloves with a polyurethane coating are thin, flexible, and breathable.
This type of coating provides a good, dry grip, and resists abrasion. A PU coating is ideal for drier applications where no oil is used.
Nitrile and nitrile foam
Thanks to a nitrile coating, the wearer of the glove has an excellent grip when working with liquids such as oil and grease.
This material prevents liquids from passing through the glove and making the hands moist.
Nitrile foam promotes the grip required for safe handling of slippery objects. Both of these coatings are combined in some gloves.
A nitrile (foam) coating provides good protection against cuts and perforations.
Latex
Latex coatings are often used in gloves that require very good abrasion resistance.
This coating is also very suitable for winter gloves thanks to its water-repellent properties.
Latex is less suitable in contact with oil or grease.
The comfort of cut resistant gloves
Comfort is also a factor to consider especially when your employees wear cut-resistant gloves for a long time. You want to prevent them not wearing protective gloves because they are uncomfortable.
Of course, everyone experiences comfort in their own way. In general, the sensitivity of the fingers and the breathability of the material have a major impact on comfort.
Finger sensitivity
Gloves should be (extra) finger-sensitive, for example, when working with fine tools or small parts.
In recent years, you increasingly see finger-sensitive gloves in combination with a higher level of protection.
This enhances the comfort of the glove.
Breathable feeling
It is pleasant if gloves breathe well especially when wearing them for a long time. Perspiration can also escape better, which prevents a clammy feeling.
The material of the coating especially determines the breathability. The lighter the coating, the more comfort you will experience.
However, the temperature in each glove eventually rises, so sweating can never be completely avoided.